Printing control variables
Printing is the last process. In the printing process, if the printing effect is found not to meet the requirements, adjustments can be made to remedy the problems that have occurred. Obviously, if a defective printing plate, squeegee or other equipment is used, the desired printing effect will definitely not be achieved. After printing, drying equipment is usually used for drying. There are two kinds of dryers commonly used in screen printing, one is to use IR heat source for drying; the other is to use UV light source for curing. Regarding the printing and drying part, there are 8 main variables.
1) Net distance
Non-contact printing is a prominent feature of screen printing, that is, the screen printing plate keeps a small distance from the top of the substrate. This distance is called the screen distance. Screen printing relies on the pressure of the squeegee to bring the printing plate into contact with the substrate to complete the transfer of graphics and text. The screen distance should be kept proper, otherwise, the printing effect will be poor.
2) Peeling distance (distance from the net)
Peeling distance refers to the distance between the screen and the substrate after the squeegee scrapes the ink across a certain area of the printing plate image. Under ideal circumstances, the peeling distance does not need to be adjusted, and the screen distance can be used to easily separate the printing plate from the substrate. However, if the ink is too thick or printing a large area, the printing plate and the substrate may not be separated quickly, resulting in blurred images. In these cases, the distance from the grid must be fine-tuned, but the amount of adjustment must not be too large, otherwise it will cause image distortion.
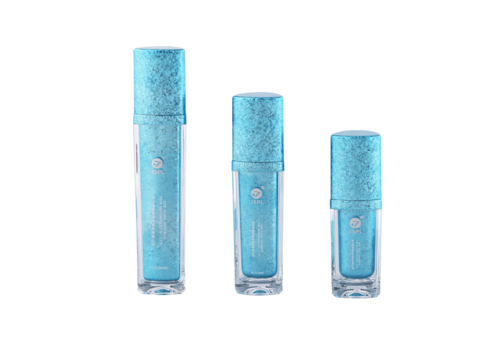
3) Flatness of printing plate
To make the printing quality stable and consistent, the flatness of the printing plate table is very important. Any depressions and protrusions on the table will adversely affect the printing quality.
4) The parallelism between the printing plate table and the screen
The distance between the screen and the surface of the entire printing plate table must be consistent. When measuring the screen distance before printing, it must be measured at multiple points.
5) Color sequence
In multi-color printing, color order is a key variable. The order of image printing has an important influence on the quality of the final print. The color sequence of printing depends on the accuracy of the printed matter, the material of the substrate and the saturation of the pattern.
6) Curing temperature
For solvent-based inks or water-based inks, increasing the drying temperature can shorten the drying time. But if the set temperature is too high, it will affect the dimensional stability of the substrate.
7) UV light intensity
UV ink should be dried with UV light. The UV light intensity is high, the curing speed is fast, and the intensity is low, the curing speed is slow. So choose the right light intensity. The spectral distribution of the UV light source should correspond to the characteristics of the UV ink used, otherwise, no matter how long the drying time is, the ink layer will not be completely dried.
8) curing time
The curing speed of the ink affects the quality of the ink after curing, and the curing speed must be adjusted according to the curing temperature and the light intensity of the UV lamp to completely cure the ink film. The curing quality of the printed product depends on the curing speed, curing temperature and the power adjustment of the UV lamp.
Surroundings
The working environment of screen printing has a direct impact on the printing results, especially high-quality printed matter must be printed and dried under a stable temperature and humidity environment. If constant temperature and humidity cannot be guaranteed, it is necessary to monitor environmental changes and provide compensation. There are two variables that affect the printing environment.
1) Pollutants in the air
There are various pollutants in the screen printing workshop, such as dust and fluff, which have an impact on the printing quality. A clean environment can eliminate these problems
2) Ambient temperature and humidity
In the plate making workshop and printing workshop, any changes in temperature and humidity will have an impact on the printing quality. If the constant temperature and humidity cannot be reached, other variables must be flexibly adjusted according to the changes in temperature and humidity. Although cumbersome, it can save money.
In addition to effectively controlling and handling the many factors that affect screen printing quality described in this article, training high-quality operators, establishing complete process management procedures, and quantitatively controlling various variables can effectively improve printing quality. Enterprises bring economic benefits.